Production sites
SEKO Group
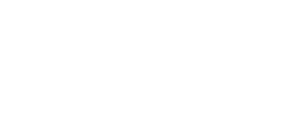
SEKO Aerospace & Power stands as the principal organizational unit within the SEKO Group, comprising two factories located in Louny and Olomouc. The Louny facility specializes in manufacturing components for the energy industry, while the Olomouc facility is dedicated to producing components for aircraft engines.
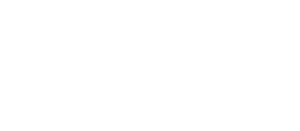
SEKO Tool, situated in Rychnov nad Kněžnou, serves as a Manufacturing site specializing in the production of cutting tools, molds, gauges, and fixtures.
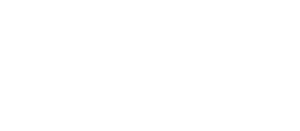
SEKO Do Brasil stands as a thriving joint venture with the esteemed Brazilian company Manuita Do Brasil, specializing in the production of steam turbine products and making significant strides into the Brazilian and South American markets.
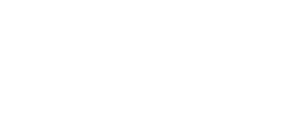
SEKO SHIVAM Engitech, a globally-reaching manufacturing facility in Vadodara, India, focuses on manufacturing stator and rotor components for steam turbines, along with manufacturing compressor wheels.
SEKO Group
SEKO Group’s companies play an important role in manufacturing critical components for aircraft engines and APUs, steam turbines, hydroelectric power plants, and complete drilling rigs, providing components to many customers worldwide. In addition, We are involved in the production of pressed components, cutting tools, and other industry-related products.
Our approach involves overseeing projects comprehensively, assuming either a supportive role or taking full responsibility for all aspects of production. This includes engaging in highly technical and technologically demanding manufacturing processes, placing SEKO Group at the top of advanced companies globally.
My journey with SEKO began in 1991, starting with a single EDM machine financed through credit, which I personally operated with my sons. The turning point came in 1997 when we successfully entered the market for steam turbine production, followed by our expansion into the aviation sector a year later by manufacturing components for aircraft engines.
Currently, we operate six facilities, four located in the Czech Republic and other three internationally. The two Czech factories in Louny specialize in producing components for power turbines, while the Olomouc facility focuses on aerospace industry components. The Rychnov nad Kněžnou Site is dedicated to manufacturing stamping tools. Our foreign facilities in Brazil and India contribute to the production of components for steam turbines. Additionally, we maintain business representation in various countries.
The technically and technologically demanding nature of our production processes positions SEKO Group as a leader in advanced manufacturing within the Czech Republic and beyond. We remain true to our original values, continuously evolving them. Our corporate policy is focused on achieving the highest quality in all our outputs, with a commitment to ensuring customer satisfaction. Over the years, we have consistently upheld our position as a prime supplier of components for the aviation and energy industries. By continually renewing our manufacturing technology in line with the latest trends, we create modern products that not only meet customer requirements but also adhere to applicable technical standards.
Vlastimil Sedláček
CEO at SEKO Aerospace

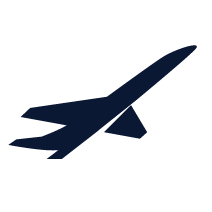

Quality
SEKO Aerospace’s objective is to effectively address the needs and requirements of all customers, harnessing the knowledge and experience of its workforce, along with insights from customers and suppliers. To realize this goal, the company commits to:
Ensuring a consistent quality in all delivered products and services.
Meeting the expectations of customers and stakeholders through collaborative efforts, thereby cultivating a circle of loyal clients, fostering a positive company reputation, and attracting new customers.
Enhancing supplier-customer relationships and actively engaging customers and suppliers within the SEKO Group in the ongoing process of improving the quality of delivered products and services.
Quality and inspection
The quality of the materials used is determined by customer requirements. The material selection encompasses its wide range, primarily including stainless steels, nickel base alloys, titanium or tungsten components, and many other materials. Inspection of finished products is carried out as needed using various manual measuring instruments and coordinate measuring machines (CMM) such as the 3D Dea Global, Nikon or 3D Optical Werth Scope. Non-destructive testing is also available. We are also capable of validating drawing characteristics using our designed inspection fixtures.
Standards
We have access to international standards, as well as a comprehensive database of metals. We adhere to material standards, test standards, special process standards, and many others. We meet customer requirements and comply with the standards they specify.
Corporate standards
Corporate standards define the basic operation of all internal processes. Our company’s internal directives are defined and in conformity to the AS 9100 standard.
AS 9100 is a standard for companies producing products for the aerospace industry, including FAIR (First Article Inspection reports), which involves a 100% inspection of the first piece from a batch and many other quality tools that ensure a high standard of product quality.
Patents
Several manufacturing processes are protected by patent office due to their exclusivity. Newly emerging ideas of strategic importance are similarly protected.
Sustainability
Management of SEKO Aerospace, a.s. commits to the following policy to reduce the company’s greenhouse gas emissions:
We recognise the value of the environment and the importance of changing the Earth’s climate system.
We commits to reducing greenhouse gas emissions in Scope 1 and Scope 2 through improving energy efficiency and installing own renewable sources of electricity.
We comply with legislative requirements related to environmental and climate protection.
We continue to take environmentally friendly measures such as using surplus heat from machines for heating, using our own water sources, maintaining greenery and other ecological features in the company’s outdoor areas.
We communicate our climate change mitigation measures publicly and to all relevant stakeholders.
Certificates
The ISO 9001 certificate is a fundamental quality system certificate, which is now a standard for almost all companies.
The AS9100D certificate is an extended version of ISO 9001 focused on aviation and astronautics.
The NADCAP certificate is a narrowly specialized certificate for special processes. It is an international certification which guarantee the stability of special processes. In the case of SEKO Aerospace, it pertains to EDM (Electrical Discharge Machining) cutting and EDM drilling. This certificate attests to our ability to maintain a high standard of quality in the products we supply to Honeywell Aerospace. We are also NADCAP certified for FPI control process. This meets requirements for several OEMs such as Pratt and Whitney, Safran, Honeywell Aerospace or GE Aerospace.
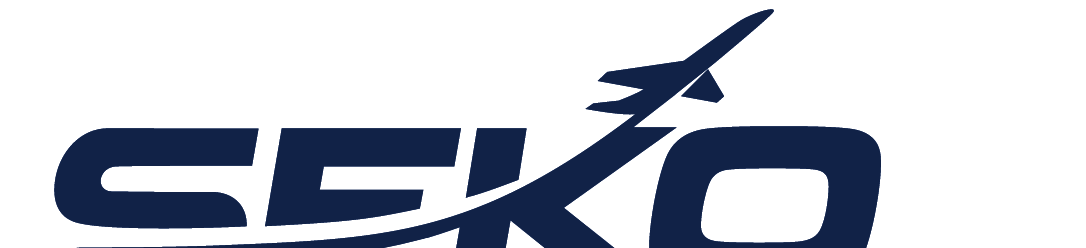